Together, the two Spanish companies will outline plans for eVTOL aircraft and operations integration in Europe and Latin America to ensure compatible interaction and maximize aircraft performance.
Following DOA approval, Lilium shifts from the design phase to industrialization, including fuselage matching and joining and a ramp-up of parts production from Tier 1 aerospace suppliers. Ecr Direct Roving For Tubing
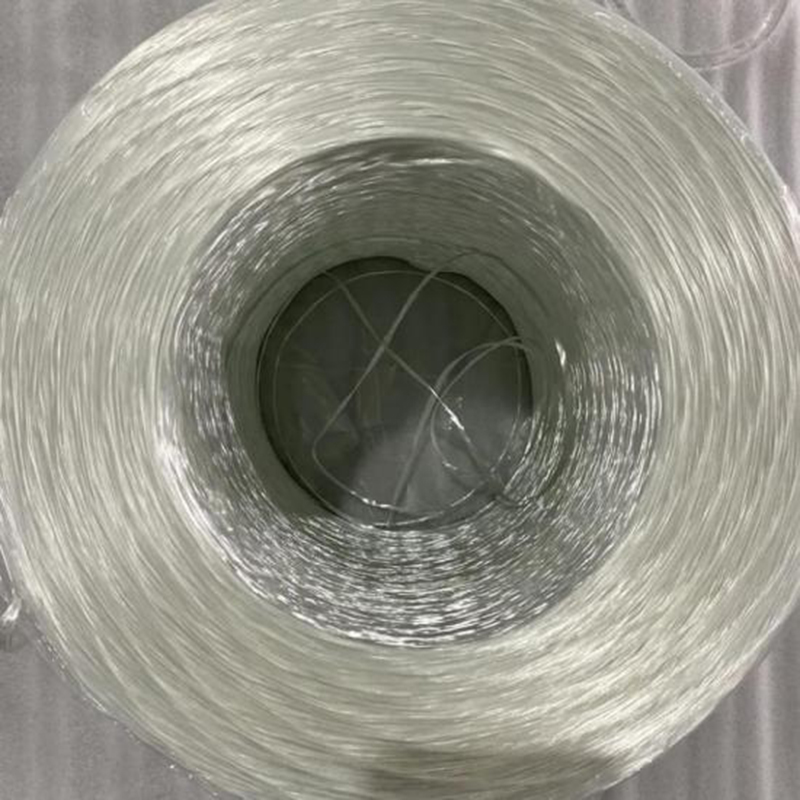
The composites-intensive electric aircraft was purchased to meet the airline’s goal of flying a commercial demonstrator by 2026.
The $37 million contract will enable Piasecki to demonstrate its ARES tilt-duct VTOL aircraft and hydrogen fuel cell propulsion technologies.
Design Organization Approval makes Lilium qualified to design and hold a type certificate for aircraft developed according to the EASA’s SC-VTOL safety objective rules.
The two-seat EL-2 Goldfinch is a blown-lift aircraft filling the gap for air travel routes between 50-500 miles. Certification and entry into service is targeted for 2028.
Combined LSAM and five-axis CNC milling capabilities will optimize D-Composites’ production services, flexibility and cut time and cost for composite tooling manufacture.
Evaluation of CFRTP m-pipe through Element’s U.K. facility aims to qualify the system for new operating environments.
Innovative prepreg tooling is highly drapable, capable of forming complex carbon fiber tooling shapes, in addition to reducing through thickness porosity and only requiring one debulk during layup.
Simutence and Engenuity demonstrate a virtual process chain enabling evaluation of process-induced fiber orientations for improved structural simulation and failure load prediction of a composite wing rib.
3D imaging and analysis capability illustrates detailed, quality characterization and performance simulation of composites and other advanced materials that properly captures the as-manufactured component.
Latest version of comprehensive simulation software speeds up computations and introduces surrogate model functionality.
Torayca-based aerospace components have successfully been repurposed into the Lenovo ThinkPad X1 Carbon Gen 12, highlighting the ongoing application of recycled composites.
Novel method for fiber-to-fiber recycling of used textiles and a low-cost, cost-effective precursor for carbon fiber manufacture earn 2023 Walter Reiners Foundation Awards.
Components critical to a bobsled’s functionality — push handles, hand grips and seats — were tailored from Windform materials, heightening both performance and safety for athletes’ racing in the 2026 Winter Olympics.
The inaugural CW From the Archives revisits Sara Black’s 2007 story on out-of-autoclave infusion used to fabricate the massive composite upper cargo door for the Airbus A400M military airlifter.
Binder-free ECTFE-apertured reinforcement maintains a high resistance against chemicals and abrasion at high temperatures, extending performance and integrity of composite systems.
Qarbon Aerospace will focus on the design, development and manufacture of a thermoplastic composite structure for defense aviation components requiring icing protection.
The novel large-format Flexbot Research XL platform enables TGS to offer 3D printing services, making use of a versatile composite material range.
Startup Fited and Brightlands Materials Center have developed a lighter weight, thinner CFRP corrective brace, including pressure sensors made from continuous carbon fibers.
Components critical to a bobsled’s functionality — push handles, hand grips and seats — were tailored from Windform materials, heightening both performance and safety for athletes’ racing in the 2026 Winter Olympics.
The inaugural CW From the Archives revisits Sara Black’s 2007 story on out-of-autoclave infusion used to fabricate the massive composite upper cargo door for the Airbus A400M military airlifter.
Combined LSAM and five-axis CNC milling capabilities will optimize D-Composites’ production services, flexibility and cut time and cost for composite tooling manufacture.
New developments regarding productivity, maintenance and ergonomics make this enhanced composite placement system well suited for the production of complex parts.
CW explores key composite developments that have shaped how we see and think about the industry today.
Knowing the fundamentals for reading drawings — including master ply tables, ply definition diagrams and more — lays a foundation for proper composite design evaluation.
As battery electric and fuel cell electric vehicles continue to supplant internal combustion engine vehicles, composite materials are quickly finding adoption to offset a variety of challenges, particularly for battery enclosure and fuel cell development.
Performing regular maintenance of the layup tool for successful sealing and release is required to reduce the risk of part adherence.
Increasingly, prototype and production-ready smart devices featuring thermoplastic composite cases and other components provide lightweight, optimized sustainable alternatives to metal.
Interest in higher performance and more sustainability drive new composite materials innovations in sporting goods and other consumer products.
Manufacturers often struggle with production anomalies that can be traced back to material deviations. These can cause fluctuations in material flow, cooling, and cure according to environmental influences and/or batch-to-batch variations. Today’s competitive environment demands cost-efficient, error-free production using automated production and stable processes. As industries advance new bio-based, faster reacting and increased recycled content materials and faster processes, how can manufacturers quickly establish and maintain quality control? In-mold dielectric sensors paired with data analytics technology enable manufacturers to: Determine glass transition temperature in real time Monitor material deviations such as resin mix ratio, aging, and batch-to-batch variations throughout the process Predict the influence of deviations or material defects during the process See the progression of curing and demold the part when the desired degree of cure, Tg or crystallinity is achieved Document resin mix ratios using snap-cure resins for qualification and certification of RTM parts Successful case histories with real parts illustrate how sensXPERT sensors, machine learning, and material models monitor, predict, and optimize production to compensate for deviations. This Digital Mold technology has enabled manufacturers to reduce scrap by up to 50% and generated energy savings of up to 23%. Agenda: Dealing with the challenge of material deviations and production anomalies How dielectric sensors work with different composite resins, fibers and processes What is required for installation Case histories of in-mold dielectric sensors and data analytics used to monitor resin mixing ratios and predict potential material deviations How this Digital Mold technology has enabled manufacturers to optimize production, and improve quality and reliability
SolvaLite is a family of new fast cure epoxy systems that — combined with Solvay's proprietary Double Diaphragm Forming technology — allows short cycle times and reproducibility. Agenda: Application Development Center and capabilities Solutions for high-rate manufacturing for automotive Application examples: battery enclosures and body panels
OEMs around the world are looking for smarter materials to forward-think their products by combining high mechanical performance with lightweight design and long-lasting durability. In this webinar, composite experts from Exel Composites explain the benefits of a unique continuous manufacturing process for composites profiles and tubes called pull-winding. Pull-winding makes it possible to manufacture strong, lightweight and extremely thin-walled composite tubes and profiles that meet both demanding mechanical specifications and aesthetic needs. The possibilities for customizing the profile’s features are almost limitless — and because pull-winding is a continuous process, it is well suited for high volume production with consistent quality. Join the webinar to learn why you should consider pull-wound composites for your product. Agenda: Introducing pull-winding, and how it compares to other composite manufacturing technologies like filament winding or pultrusion What are the benefits of pull-winding and how can it achieve thin-walled profiles? Practical examples of product challenges solved by pull-winding
Composite systems consist of two sub-constituents: woven fibers as the reinforcement element and resin as the matrix. The most commonly used fibers are glass and carbon, which can be processed in plane or satin structures to form woven fabrics. Carbon fibers, in particular, are known for their high strength/weight properties. Thermoset resins, such as epoxies and polyurethanes, are used in more demanding applications due to their high physical-mechanical properties. However, composites manufacturers still face the challenge of designing the right cure cycles and repairing out-of-shelf-life parts. To address these issues, Alpha Technologies proposes using the encapsulated sample rheometer (premier ESR) to determine the viscoelastic properties of thermosets. Premier ESR generates repeatable and reproducible analytical data and can measure a broad range of viscosity values, making it ideal for resins such as low viscous uncured prepreg or neat resins as well as highly viscous cured prepregs. During testing, before cure, cure and after cure properties can be detected without removing the material from the test chamber. Moreover, ESR can run a broad range of tests, from isothermal and non-isothermal cures to advanced techniques such as large amplitude oscillatory shear tests. During this webinar, Alpha Technologies will be presenting some of the selected studies that were completed on epoxy prepreg systems utilizing ESR and how it solves many issues in a fast and effective way. It will highlight the advantages of this technique that were proven with the work of several researchers. Moreover, Alpha Technologies will display part of these interesting findings using the correlations between the viscoelastic properties such as G’ and mechanical properties such as short beam shear strength (SBS).
Surface preparation is a critical step in composite structure bonding and plays a major role in determining the final bonding performance. Solvay has developed FusePly, a breakthrough technology that offers the potential to build reliable and robust bonded composite parts through the creation of covalently-bonded structures at bondline interface. FusePly technology meets the manufacturing challenges faced by aircraft builders and industrial bonding users looking for improved performance, buildrates and lightweighting. In this webinar, you will discover FusePly's key benefits as well as processing and data. Agenda: Surface preparation challenges for composite bonding FusePly technology overview Properties and performance data
The incorporation of EMI shielding into composites is necessary in a wide range of applications — such as electronics and battery enclosures for AAM, automotive and aerospace — where EMI could interfere with the operation of the device, vehicle or aircraft, ultimately compromising security and control. TFP’s conductive nonwoven materials provide a solution, possessing a combination of properties that make them highly infusible, flexible, lightweight and an effective EMI shield. This combination allows them to overcome challenges in both application and process that more traditional substrates such as films, foils and paints struggle to achieve. In this webinar, Dr. Mark James will introduce TFP’s conductive nonwovens, their lightweight structure and EMI shielding capability. He will discuss how they are easily incorporated into composites to impart this functionality to the surface of a part, with some typical examples. Mike Campbell and Adam Halsband will then provide a case study on a new development for TFP materials as an EMI enhanced SMC compound. This compound is designed as a scalable, cost-effective solution for high throughput BEV applications, such as battery enclosures. Agenda: An introduction to TFP’s conductive nonwovens, their structure and manufacture The key physical properties and how they are tailored to suit end-use requirements How conductive nonwovens can be used effectively in a variety of applications A case study on the development and use of TFP’s veils in an EMI enhanced SMC compound for BEV applications
The annual Conference on Composites, Materials, and Structures (also known as the Cocoa Beach Conference) is the preeminent export controlled and ITAR restricted forum in the United States to review and discuss advances in materials for extreme environments. The Conference started in the 1970s as a small informal gathering for government and industry to share information on programs and state-of-the-art technology. Attendance has grown to nearly 500 people while preserving this same objective to share needs and trends in high-temperature and extreme environment materials, and the latest information on advanced materials and manufacturing processes. The five-day conference program includes two to three parallel sessions per day on topics including thermal protection materials, ceramic matrix composites, carbon-carbon materials, ballistic technologies, hypersonics, and gas turbine engines. Attendees are engineers, scientists, managers, and operational personnel from the turbine engine, aviation, missiles and space, and protective equipment communities. These communities include the Navy, Air Force, Army, MDA, NASA, DARPA, FAA, DOE, engine manufacturers, missile and aircraft manufacturers, commercial space companies, and material and component suppliers. The Conference will be held in St. Augustine again for 2024! Participation is limited to U.S. Citizens and U.S. Permanent Residents only with an active DD2345 certification.
The 48th International Conference & Exposition on Advanced Ceramics & Composites (ICACC 2024) will be held from Jan. 28–Feb. 2, 2024, in Daytona Beach, Fla. It is a great honor to chair this conference, which has a strong history of being one of the best international meetings on advanced structural and functional ceramics, composites, and other emerging ceramic materials and technologies.
The Transformative Vertical Flight (TVF) 2024 meeting will take place Feb. 6–8, 2024 in Santa Clara, California, in the heart of Silicon Valley and will feature more than 100 speakers on important progress on vertical takeoff and landing (VTOL) aircraft and technology.
The Program of this Summit consists of a range of 12 high-level lectures by 14 invited speakers only. Topics are composite related innovations in Automotive & Transport, Space & Aerospace, Advanced Materials, and Process Engineering, as well as Challenging Applications in other markets like Architecture, Construction, Sports, Energy, Marine & more.
JEC World in Paris is the only trade show that unites the global composite industry: an indication of the industry’s commitment to an international platform where users can find a full spectrum of processes, new materials, and composite solutions.
Charting the Skies of Tomorrow: The Sustainable Aviation Revolution Welcome to a new era of air travel where innovation meets sustainability. Electric, hybrid-electric and hydrogen-powered aircraft represent a promising path to reach climate neutrality goals, with the aviation industry and governments jointly pushing boundaries to bring disruptive aircraft into service by 2035. From cutting-edge technologies to revamped regulations and greener airports, the pursuit of sustainable aviation requires unparalleled collaboration throughout the whole aviation value chain and ecosystem. Join us at the Clean Aviation Annual Forum from 5 until 6 March 2024, as we navigate towards cleaner skies together.
Thousands of people visit our Supplier Guide every day to source equipment and materials. Get in front of them with a free company profile.
Initial demonstration in furniture shows properties two to nine times higher than plywood, OOA molding for uniquely shaped components.
The composite tubes white paper explores some of the considerations for specifying composite tubes, such as mechanical properties, maintenance requirements and more.
Foundational research discusses the current carbon fiber recycling landscape in Utah, and evaluates potential strategies and policies that could enhance this sustainable practice in the region.
In its latest white paper, Exel navigates the fire, smoke and toxicity (FST) considerations and complexities that can influence composites design.
New white paper authored by Eike Langkabel, Sebastian de Nardo, and Jens Bockhoff, examines the best resin formulations for composites used in automotive part production, both structural parts and body panels.
Tension control plays a vital role in composites manufacturing in order to achieve automated processing, continuous processing, reduced scrap, increased product quality, and more, says a new white paper released by The Montalvo Corp.
Austrian research institute Wood K plus makes 95% silicon carbide ceramics more sustainable (>85% bio/recycled content), enables 3D shapes via extrusion, injection molding and 3D printing.
Thermoplastic polymer resin was designed to tackle distinctive industry challenges of large-scale 3D printing while also assisting with sustainability initiatives.
The MB9, representing a combination of high performance and eco-conscious materials use, will be commercially available in time for the 2024 sailing season.
For 42 months, the Aitiip Technology Center will coordinate the EU-funded project to design a new range of intermediate materials, such as pellets or resin-impregnated carbon fibers, which will be used to manufacture more sustainable final products.
Co-located R&D and production advance OOA thermosets, thermoplastics, welding, recycling and digital technologies for faster processing and certification of lighter, more sustainable composites.
The German Institutes of Textile and Fiber Research are targeting more sustainable carbon fiber via low-pressure stabilization and bio-based precursors, and working with Saint-Gobain to commercialize oxide ceramic fibers for CMC.
Explore the cutting-edge composites industry, as experts delve into the materials, tooling, and manufacturing hurdles of meeting the demands of the promising advanced air mobility (AAM) market. Join us at CW Tech Days to unlock the future of efficient composites fabrication operations.
CW’s editors are tracking the latest trends and developments in tooling, from the basics to new developments. This collection, presented by Composites One, features four recent CW stories that detail a range of tooling technologies, processes and materials.
This CW Tech Days event will explore the technologies, materials, and strategies that can help composites manufacturers become more sustainable.
The composites industry is increasingly recognizing the imperative of sustainability in its operations. As demand for lightweight and durable materials rises across various sectors, such as automotive, aerospace, and construction, there is a growing awareness of the environmental impact associated with traditional composite manufacturing processes.
CompositesWorld’s CW Tech Days: Infrastructure event offers a series of expert presentations on composite materials, processes and applications that should and will be considered for use in the infrastructure and construction markets.
In the Automated Composites Knowledge Center, CGTech brings you vital information about all things automated composites.
During CW Tech Days: Thermoplastics for Large Structures, experts explored the materials and processing technologies that are enabling the transition to large-part manufacturing.
Closed mold processes offer many advantages over open molding. This knowledge center details the basics of closed mold methods and the products and tools essential to producing a part correctly.
CompositesWorld’s CW Tech Days: Infrastructure event offers a series of expert presentations on composite materials, processes and applications that should and will be considered for use in the infrastructure and construction markets.
Explore the cutting-edge composites industry, as experts delve into the materials, tooling, and manufacturing hurdles of meeting the demands of the promising advanced air mobility (AAM) market. Join us at CW Tech Days to unlock the future of efficient composites fabrication operations.
Thermoplastics for Large Structures, experts explored the materials and processing technologies that are enabling the transition to large-part manufacturing.
MVP's Automated Equipment: Revolutionizing Composites Part Production Through Filament Winding within CompositesWorld's CompositesWorld Collections Knowledge Center
Composites One Offers Manufacturing Efficiencies with Aerovac Kitting Solutions within CompositesWorld's CompositesWorld Collections Knowledge Center
A report on the demand for hydrogen as an energy source and the role composites might play in the transport and storage of hydrogen.
This collection features detail the current state of the industry and recent success stories across aerospace, automotive and rail applications.
This collection details the basics, challenges, and future of thermoplastic composites technology, with particular emphasis on their use for commercial aerospace primary structures.
This collection features recent CW stories that detail a range of tooling technologies, processes and materials.
The structural properties of composite materials are derived primarily from the fiber reinforcement. Fiber types, their manufacture, their uses and the end-market applications in which they find most use are described.
The structural properties of composite materials are derived primarily from the fiber reinforcement. In a composite, the fiber, held in place by the matrix resin, contributes tensile strength, enhancing performance properties in the final part, such as strength and stiffness, while minimizing weight. Fiber properties are determined by the fiber manufacturing process and the ingredients and coating chemistries used in the process.
The majority of all fibers used in the composites industry are glass. Glass fibers are the oldest and, by far, the most common reinforcement in most end-market applications (the aerospace industry is a significant exception) to replace heavier metal parts. Glass fiber weighs more than the second most common reinforcement, carbon fiber, and is not as stiff, but is more impact-resistant and has a greater elongation-to-break (that is, it elongates to a greater degree before it breaks). Depending upon the glass type, filament diameter, coating chemistry (called “sizing,” see “Critical fiber sizing," below) and fiber form, a wide range of properties and performance levels can be achieved.
To make glass fiber, raw materials are melted and drawn into delicate and highly abrasive filaments, ranging in diameter from 3.5 to 24 μm. Silica sand is the primary raw ingredient, typically accounting for more than 50% of glass fiber weight. Metal oxides and other ingredients can be added to the silica, and processing methods can be varied to customize the fibers for particular applications.
Continuous glass filaments are supplied in bundles called strands. Roving generally refers to a bundle of untwisted strands, packaged, like thread, on a large spool. Single-end roving consists of strands that are made up of multiple continuous glass filaments that run the length of the strand. Multiple-end roving contains lengthy but not entirely continuous strands, which are added or dropped in a staggered arrangement during the spooling process. Yarn is a collection of strands that are twisted together.
Electrical or E-glass, so named because its chemical composition makes it an excellent electrical insulator, is particularly well-suited to applications in which radio-signal transparency is desired, such as aircraft radomes, antennae and printed circuit boards (PCBs; see CW’s report on the shifting role of glass fiber reinforcement in PCBs: “Printed circuit boards: A mobile market,”). However, it is also the most economical glass fiber for composites, offering sufficient strength to meet the performance requirements in many applications at a relatively low cost. It has become the standard form of fiberglass, accounting for more than 90% of all glass-fiber reinforcements. At least 50% of E-glass fibers are made up of silica oxide; the balance comprises oxides of aluminum, boron, calcium and/or other compounds, including limestone, fluorspar, boric acid and clay.
When greater strength is desired, high-strength glass, first developed for military applications in the 1960s, is an option. Known by several names — S-glass in the US, R-glass in Europe and T-glass in Japan, its strand tensile strength is approximately 700 ksi, with a tensile modulus of up to 14 Msi. S-glass has appreciably greater silica oxide, aluminum oxide and magnesium oxide content than E-glass and is 40-70% stronger than E-glass.
E-glass and S-glass lose up to half of their tensile strength as temperatures increase from ambient to 540°C, although both fiber types still exhibit generally good strength in this elevated temperature range. Manufacturers are continually tweaking S-glass formulations. An S-3 UHM (for ultra-high modulus) Glass, for example, was introduced by AGY Holding Corp. (Aiken, SC, US) several years ago. The upgraded S-3 glass has a tensile modulus of 14,359 — higher than S-glass and 40% higher than E-glass — due to improved fiber manufacturing as well as proprietary additives and melt chemistry.
Although glass fibers have relatively high chemical resistance, they can be eroded by leaching action when exposed to water. For example, an E-glass filament 10μ in diameter typically loses 0.7% of its weight when placed in hot water for 24 hours. The erosion rate, however, slows significantly because the leached glass forms a protective barrier on the outside of the filament; only 0.9% total weight loss occurs after seven days of exposure. To slow erosion, moisture-resistant sizings, such as silane compounds, are applied during fiber manufacturing.
Corrosion-resistant glass, known as C-glass or E-CR glass, stands up better to an acid solution than does E-glass. However, E-glass and S-glass are much more resistant to sodium carbonate solution (a base) than is C-glass. A boron-free glass fiber, with performance and price comparable to E-glass, demonstrates greater corrosion resistance in acidic environments (similar to that of E-CR glass), higher elastic modulus and better performance in high temperatures than does E-glass. In addition, taking boron out of the manufacturing process produces fewer environmental impacts, a decided advantage.
High-performance fibers used in advanced composites include carbon fiber, aramid fiber (known by the trade names Kevlar and Twaron), boron fibers, high-performance polypropylene fiber, ultra high molecular weight polyethylene (PE), newer fibers such as poly p-phenylene-2,6-benzobisoxazole (PBO), and hybrid combinations, as well.
The fiber is the composite's primary source of the strength and stiffness. Fibers must be treated with chemicals, called sizings, that make them compatible with the intended matrix and ease processing. These rolls contain Tenax carbon fiber filament yarn, recently introduced by Toho Tenax Europe GmbH (Wuppertal, Gemany) with a new tailored sizing that makes the fibers compatible with thermoplastic resin matrices and useful in high-temperature composites applications. Source: Toho Tenax
Carbon fiber — by far the most widely used fiber in high-performance applications — is produced from a variety of precursors, including polyacrylonitrile (PAN), rayon, pitch as well as bio-based, carbon-rich precursors such as lignin or bio-based PAN. The precursor fibers are chemically treated, heated and stretched, then carbonized, to create the high-strength fibers. The first high-performance carbon fibers on the market were made from rayon precursor. PAN-based carbon fibers have long since replaced rayon in structural applications, but the latter’s “dogbone” cross-section and high-temperature performance often makes it the fiber of choice for carbon/carbon (C/C) composites in ablative heat shields. PAN-based carbon fibers are the most versatile and widely used. They offer an amazing range of properties, including excellent strength — to 1,000 ksi — and high stiffness. Pitch fibers, made from petroleum or coal tar pitches, have high to extremely high stiffness and low to negative axial coefficient of thermal expansion (CTE). Their CTE properties are especially useful in spacecraft applications that require thermal management, such as electronic instrument housings. Carbon fiber’s properties are stimulating searches for alternative and less expensive precursor materials, such as lignin derived from pulp and paper waste. Research efforts are gaining traction for such low-cost fiber materials and they are on the way to becoming viable commercial reinforcement choices, thanks to research efforts at Oak Ridge National Laboratory (Oak Ridge, TN, US) and other groups.
Although they are stronger than glass or aramid fibers, carbon fibers are not only less impact-resistant but also can cause galvanic corrosion in metals they contact, because of their electrical conductivity. Fabricators overcome the latter problem by using a barrier material or veil ply — often fiberglass/epoxy — during laminate layup.
The basic fiber form for high-performance carbon fiber is bundles of continuous fibers called tows. A carbon fiber tow consists of thousands of continuous, untwisted filaments, with the filament count designated by a number followed by “K,” indicating multiplication by 1,000 (e.g., 12K indicates a filament count of 12,000). Tows may be used directly, in processes such as filament winding or pultrusion, or may be converted into unidirectional tape, fabric and other reinforcement forms (for more about fiber forms, see “Fiber reinforcement forms.”
“Spread tow” fabrics are gaining popularity. As the name implies, the filaments in each tow are spread out to form very thin, wide “tapes” that are then woven. Such fabrics deliver very good performance at very low weight. Oxeon (Borås, Sweden) is a well-known purveyor of spread-tow fabrics, tradmarked TeXtreme, and other fiber converters are following suit.
Aramid fibers, formed from aromatic polyamide, provide exceptional impact resistance and good elongation (higher than carbon, but less than glass). Standard, high-performance aramid fiber has a modulus of about 20 Msi, tensile strength of approximately 500 ksi and elongation of nearly 3%.
Renowned for its performance in bulletproof vests and other armor and ballistic applications, aramid fiber has been in demand in part due to the need for personnel protection and armor in law-enforcement and military markets. Aramid’s properties also make the fiber an excellent choice for helicopter rotor blades, marine vessel hulls and sporting goods where impact resistance is desired.
Boron fibers are five times as strong and twice as stiff as steel. They are made by a chemical vapor deposition process in which boron vapors are deposited onto a fine tungsten or carbon filament. Boron provides strength, stiffness and light weight, and possesses excellent compressive properties and buckling resistance. Uses for boron composites range from sporting goods, such as fishing rods, golf club shafts, skis and bicycle frames, to aerospace applications as varied as aircraft empennage skins, truss members and prefabricated aircraft repair patches.
Commercially available ultra high-molecular weight (UHMW) polyethylene (PE) fibers are well known for their extremely light weight, excellent chemical and moisture resistance, outstanding impact resistance, antiballistic properties and low dielectric constant. However, PE fibers have relatively low resistance to elongation under sustained loading, and the upper limit of their use temperature range is about 98°C. PE fiber composites are used in racing boat hulls, ski poles, offshore mooring ropes and other applications that require impact and moisture resistance and light weight but do not need extreme temperature resistance. At least one aircraft manufacturer uses high-modulus PE fibers for the bulletproof insert in cockpit doors.
High-performance polypropylene (PP) fiber is a fairly new olefin-based fiber type for composites, and is produced by Innegra Technologies (Greenville, SC, US) and marketed as Innegra fiber. It is being adopted in applications that exploit its light weight, high ductility and toughness, impact resistance and vibration damping properties. Innegra is often woven into a hybrid fabric with other high-performance fibers to increase material toughness.
Poly p-phenylene-2,6-benzobisoxazole (PBO), known by its trade name Zylon, is a relatively new fiber with modulus and tensile strength almost double that of aramid fiber and a decomposition temperature that is almost 100°C higher. Suitable for high-temperature applications, it is currently used in protective ballistic armor, sporting goods, insulation and tire reinforcements.
The high cost of high-performance fibers can be a deterrent to their selection, if manufacturers neglect to examine how that high cost is mitigated by the greater performance, durability and design freedom these materials bring to a project and the consequent positive effects those advantages have on a key metric: lifecycle cost. This is particularly true for carbon fiber, the selection of which has, historically, been complicated by significant fluctuations in carbon fiber supply and demand. Carbon and other high-performance fibers generate perennially high interest in the state of global fiber markets, a subject treated annually in the SourceBook's "Supply and demand: Advanced fibers" feature. The SourceBook's publisher, CompositesWorld, also offers the yearly Carbon Fiber conference, devoted to examinations of those markets and applications.
Quartz fibers, while more expensive than glass, have lower density, higher strength and greater stiffness than E-glass, and about twice the elongation-to-break, making them a good choice where durability is a priority. Quartz fibers also have a near-zero coefficient of thermal expansion (CTE) and can maintain their performance properties under continuous exposure to temperatures as high as 1050°C and up to 1250°C for short time periods. Quartz fibers possess significantly better electromagnetic properties than glass, a plus when fabricating parts such as aircraft radomes that protect radar systems and other key electronic equipment.
Ceramic fibers offer high to very high temperature resistance but low impact resistance and relatively poor room-temperature properties. Typically much more expensive than other fibers, ceramic, like quartz, is the fiber of choice when its advantages justify the extra cost. One application of ceramic fibers is for flame-resistant veil material in laminates for aircraft interiors, which must withstand 1093°C for at least 15 minutes without flame penetration. Ceramic composites, which combine ceramic or silicon carbide fibers in a ceramic matrix are now being more widely adopted for use in certain high-heat aircraft engine applications. (To read more about ceramic-matrix composites in jet engines see "Aeroengine Composites, Part 1: The CMC invasion.")
Basalt fibers are inexpensive, golden brown-colored fibers, similar to glass, and historically produced in Russia and Ukraine. Kamenny Vek (Dubna, Russia), Sudaglass Fiber Technology Inc. (Houston, TX, US) and Technobasalt-Invest LLC (Kyiv, Ukraine) have been basalt fiber suppliers. A new supplier, Mafic (Kells, County Meath, Ireland), offers basalt fibers in both continuous form and as long-fiber thermoplastic pellets, and mines and produces its basalt fiber in Ireland.
Basalt reportedly exhibits somewhat better chemical and alkali resistance than glass and is said to offer an alternative to glass fiber in composite rebar used to reinforce concrete in civil infrastructure and building construction applications. Basalt’s market share, however, has decreased somewhat over the past several years due to issues with product consistency because the composition of the basalt rock from which the fibers are manufactured varies, based on the quarry from which it is extracted. That said, there is evidence from testing in Europe that basalt fiber can clearly outperform E-glass (see the article "Can basalt fiber bridge the gap between glass and carbon?"
Fiber hybrids capitalize on the best properties of more than one fiber type and can reduce raw material costs. Hybrid composites that combine carbon/aramid or carbon/glass fibers have been used successfully in ribbed aircraft engine thrust reversers, telescope mirrors, driveshafts for ground transportation vehicles, and in the infrastructure arena, in column-wrapping systems that reinforce concrete structural members.
Natural fibers — abaca, bamboo, coconut, flax, hemp, jute, kenaf and sisal are the most common — are derived from the bast or outer stem of certain plants. Natural fibers are enjoying increased use because of their very low weight, adequate structural performance, and their “green” attributes including recyclability. The latter include lower cost (less energy is expended in their production), sustainability (they are biodegradable, and renewable) and carbon dioxide neutrality. They also have the lowest density of any structural fiber but possess sufficient stiffness and strength for some applications. Read CW's article on the bio-fiber reinforcements market, "Natural fiber composites: Market share, one part at a time."
With decades of development work behind it, the natural fibers industry is maturing. Indeed, it appears to be on the verge of leveraging the products’ numerous cost, performance and environmental benefits to big-time technical and potentially high-volume commercial applications. Pictured here are dyed bamboo fibers that are finding a place in highly decorated products, such a snowboards, surfboards and skis, becuase they have better damping properties than carbon fiber and are also easier and cheaper to color than glass fiber. Source | Sunstrand
The automotive industry, in particular, is using these fibers in traditionally unreinforced plastic parts and even employs them as an alternative to glass fibers in auto interiors. Natural fiber-reinforced thermosets and thermoplastics are most often found in door panels, package trays, seat backs, headliners and trunk liners in cars and trucks. European fabricators hold the lead in use of these materials, in part because regulations now require their automobile components to be almost completely recyclable, but The Ford Motor Co. (Detroit, MI, US) in the US has developed a host of natural fiber and bio-resin-based parts for its cars. Natural fibers can be incorporated into molded or extruded parts and, more recently, have been used in the direct long fiber injection (D-LFT) process where kenaf, flax and natural fiber/glass hybrids are used to reinforce polypropylene. Studies are underway to determine the suitability of long natural fiber composites for structural applications.
To achieve desirable properties in composite components, adhesion between the fiber and the matrix must be optimized. This bond at the fiber/matrix interface requires saturation of the fiber bundle with resin (termed wetout). To ensure good adhesion, attention must be given to fiber surface preparation, such as the use of a surface coating or coupling agent, termed sizing. Sizing, applied to fiber filaments immediately after their formation, actually serves two purposes: It not only enhances the fiber/matrix bond but it also provides a dry lubricant on the fiber surface that protects the fiber from abrasion and breakage during downstream handling, such as weaving or prepregging. Although it accounts for only 0.25-6.0% of total fiber weight, sizing is a dynamic force in fiber reinforcement performance.
Sizing chemistry is one of the primary attributes that distinguish each manufacturer’s fiber products from those of its competitors. It can be customized to optimize fiber performance in particular manufacturing processes, such as pultrusion, filament winding and weaving. For example, developments in sizing formulations have variously resulted in more cleanly chopped glass with reduced “fuzz” (caused by abrasion) and glass that wets out more efficiently.
Historically, carbon fiber was sized only for compatibility with epoxy resin. Today, fiber manufacturers are responding to demands from fabricators and OEMs to produce carbon fibers that are compatible with a broader range of resins and processes, as carbon fiber use increases in applications outside the aerospace arena. Many high-performance fiber producers now offer optimized sizings that are compatible with thermoplastic resins, particularly for high-speed automotive part processing.
This article was originally published 3/17/2016, updated 7/1/2022
The matrix binds the fiber reinforcement, gives the composite component its shape and determines its surface quality. A composite matrix may be a polymer, ceramic, metal or carbon. Here’s a guide to selection.
Compared to legacy materials like steel, aluminum, iron and titanium, composites are still coming of age, and only just now are being better understood by design and manufacturing engineers. However, composites’ physical properties — combined with unbeatable light weight — make them undeniably attractive.
Composites Technology Development's first commercial tank in the Type V category presages growth of filament winding in storage of compressed gases.
Options for adding color have been around for decades, but new products are hoping to up the ante and open new markets.
Although we have methods to create useful product forms from recovered fiber, creating demand for those products will require new entrepreneurial effort.
When I started writing about composites in the way, way back, industry innovator Brandt Goldsworthy was still alive. His article on basalt fiber was one of the most-read columns in the old Composites Technology book, and there seems to be a lot of interest in this alternative performance fiber. Mafic SA is a new player in the basalt fiber market.
Suppliers and adventurous composites fabricators put the “feel good” aspect in the rearview mirror, winning customers by competing on price and performance.
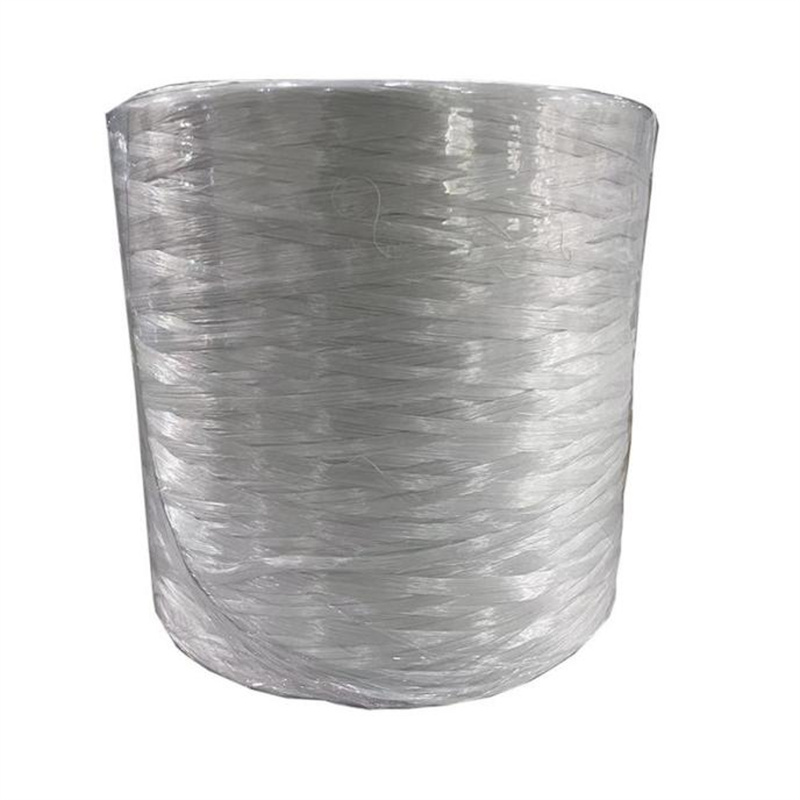
E-Glass Direct Roving For Wind Power CompositesWorld is the source for reliable news and information on what’s happening in fiber-reinforced composites manufacturing. Learn More