One day as I was driving from my home near Kraemer Lake, I noticed a small herd of cattle in a pasture fenced with barbed wire. It brought back memories. Wire had been a much-used commodity on our farm a few years back. I remember my husband, Harold, using it not just to fence in cattle, but also to hold shut gates, hold together broken machinery, hang up tools — and he even unlocked car doors with it a time or two. There was always a bit of used, rusty wire to be found somewhere.
Drive the rural byways in Central Minnesota on any given day and watch for barbed wire fences. You will undoubtedly — eventually — see a round wreath-like coil of barbed wire hanging on a post. It is the rusty remnant of a barbed wire fence from an earlier day. Security Fencing Making Machine

Life in America was reshaped by the use of the thorny fence known as “barbed wire.” This highly effective fencing material of early ranchers and farmers changed life “as dramatically as the rifle, six-shooter, telegraph, windmill and locomotive,” in words used by the U.S. National Archives & Records Administration.
Before fencing, livestock grazed freely, competing for fodder and water. Fencing put an end to this type of open foraging by roaming cattle and other livestock. Pioneers fenced the land to set common boundaries and property lines, to keep livestock out of farm fields, or to confine them within a designated area.
Early post and rail fences were built entirely of wood, using three rails and posts set 2 or more feet into the ground. Snake or angle fences lay almost entirely above ground. Both were laboriously installed, rotted over time and had to constantly be replaced.
Locally, fence posts meant extra income for area farmers. Forests and woods for fence posts and rails were plentiful in Central Minnesota but not in many south and southwestern parts of the state. Farmers in Central Minnesota met their need.
“Farmers cleared land of trees in anticipation of planting crops on more land. Much of the lumber from the trees was made into wooden fence posts,” Stan Rausch of St. Martin said in a 2014 interview. His dad, Math Rausch, operated a general store in St. Martin from the 1920s to the '70s — and for the greater part of early winters, he found a ready market for posts and rails in those parts of Minnesota where wood was not plentiful. For many years this was a certain and steady income for farmers in the area and for Rausch during the “quiet” winter months.
“A skilled woodsman could fell a dozen white oak trees, straight for 20 feet and 15 inches in diameter … and split from each four or five posts — some 120 posts — in one day of strenuous labor,” wrote Ruben L. Parson in "Ever the Land: A Homestead Chronicle."
(My father, Henry Salzl, ever a down-to-earth entrepreneur, said when he made fence posts, he kept the chips and sawdust from sharpening the posts for smoking meat when butchering time rolled around in fall.)
Eventually, barbed wire replaced wooden fences. In Minnesota, it was the least costly fence to build in terms of labor and materials, and it was effective and durable. Barbed wire consisted of a series of single twist wire, double twist, traditional twist, galvanized or PVC-coated manufactured wire. It was colloquially referred to as “barb wire” or “bob wire.”
Many history books consider wire fencing as a comparatively recent American invention, giving such dates as 1873 for the invention of single-strand barbed wire and 1883 for woven wire. Yet, Benjamin Franklin is said to have experimented with wire for enclosing cattle, hogs and sheep early in the 19th century. He read a lengthy “Account of Wire Fencing” at the Philadelphia Agricultural Society on Jan. 2, 1816.
“By then there were several Pennsylvania farms using wire fences,” wrote Eric Sloane in "A Reverence for Wood."
The first wire fences consisting of only one strand of wire were constantly broken by the weight of cattle pressing against them to get at grass on the other side of the fence. (Was it really greener there?) By the late 1800s, two-strand barbed wire came into widespread use.
Michael Kelly is credited with making a significant improvement to single-strand wire fencing, He twisted two wires together to form a cable interspaced with barbs, known as a "thorny fence." Kelly's double-strand design made fences stronger, and the painful barbs kept cattle at a distance.
Predictably, other inventors sought to improve upon Kelly's design. Among them was Joseph Glidden, a farmer from DeKalb, Illinois.
In 1873 and 1874, patents were issued for various designs similar to Kelly's invention. The eventual winner was Glidden with his design for a simple wire barb locked in place onto a double-strand wire. Glidden's design made barbed wire more effective, and he invented machinery to mass-produce it.
It quickly became standard fencing material. When used with newly invented, machine-made, wire-cut nails, fence-staples and eventually steel-fence posts, barbed wire was a much-desired product.
In the Old West barbed wire provoked range wars between grazers and intruding farmers. Sometimes border lines were disputed and had to be mediated by the local town board. They lasted only a few days or they could last longer, neighbors not speaking to each other for entire lifetimes.
In Minnesota, the 1877-1878 Legislatures legalized the use of barbed wire. Fencing kept livestock in pastures where they belonged and out of cropped fields where they could wreak havoc.
My mother, in a 1982 interview, said her family fenced in the garden and yard around the house to keep cattle and other livestock out of those areas. She said that in the Avon Hills where she grew up, “Everybody’s cattle roamed freely and would forage together. They wore bells around their necks and each family knew the sound of their own bells. The fences had to be kept in tip-top repair because if a herd of cattle walked through a garden, it was ruined for that year.”
Barbed wire fences were not work-free, however. Erecting them was a chore that required special gloves and sturdy clothing. Fortunately, fences were generally built in spring when farmers naturally wore heavier clothing but the hands always needed special protection when working with barbed wire.
Digging holes for fence posts could be difficult. Many times the shovel hit a stone. If the stone was quite large, the hole had to be moved over a foot or two. And, fences required constant mending after the first few years because wires deteriorated. Old or rusted barbed wire fencing was especially labor-intensive.
Building a barbed wire fence
Building a barbed wire fence requires some knowledge of wire as well as the landscape and some ingenuity. The builder must realize that most barbed wire has a degree of flexibility. My husband grew up and lived on a farm most of his life. He said he built — and repaired — many fences. He explained how it is done.
He said, to begin, the builder marks off the location of the fence. He then sets posts about 8 to 10 feet apart. If building the fence with wooden posts, he "stomps" a sharpened post into the ground and manually pounds it down with a 16-pound cast-iron maul. If using steel fence posts, he applies the same method but uses a T-post hole driver, a steel tool that fits snugly around the post, and with some muscle applied, forces the post into the ground.
After all the line-posts are set, he moves to the corner posts where a post-hole digger is used. This tool, shaped like a partially closed hand at the end of a handle, is used to dig a hole large enough to accommodate a larger post deeper into the ground than required for the line posts. This post is braced with horizontal posts secured in the ground.
Once all posts are set, the barbed wire, which comes in rolls, is unrolled by putting a pipe through the hole, then walking the length of the fence dropping wire as it unrolls. On one corner post is a mechanism that locks in the wire. Another tool, this one with a chain attached, is wrapped around the other corner post and a series of pullies and ropes is pulled until the wire is taut — or a metal wire stretcher is used. A mistake novice fence-builders make is tightening the wire too much. “It must have some give,” Harold said.
The wire is then fastened to the steel posts with clips or to wooden posts with staples. A fence to hold cattle is usually comprised of four strands. Once the top wire is in place, the same procedure is applied to the next three wires, about 10 inches apart. When the entire area is properly fenced in good and tight, “cattle will respect it,” he added. The wire, however, stretches over time if cattle lean against it.
Each spring a farmer walks the fence looking for breaks and stretching. Snow is hard on fences. “As snow piles up, freezing and thawing causes the wires to lose tensile strength. Rust, too, weakens barbed wire fences.”
'A little bit of fencing will make your day'
In a recent interview, Jim and Bernie Doll told me that when they bought the farm of their dreams in the early 1960s in rural Richmond, it included about 5 miles of fencing. Beef cattle they raised grazed and roamed the fenced-in pasture and woods. Some of the fencing had been built by the former owners in the early 1900s. It was old. It had rusted.
Bernie said every spring their family motto was “a little bit of fencing will make your day.” Repair was never-ending. On weekends and often on Father’s Day when the children came home to visit, they were put to work fixing fences.
Almost daily, Jim went to work at Richmond State Bank, the kids went off to school, “and I was left to chase cows. I would be washing breakfast dishes, look out the window, and see cows all over the yard. My collie dog was a big help but first I’d have to look for wire in the shed and by then the neighbors were calling that our cows were out.
“One day I thought to myself, I am a city girl. I was not put on this farm to chase cows. I called Jim at the bank and said, ‘I want a divorce.’ He came home immediately and fixed the fence and we’re still together!”
Jim said, “All the time we were fixing the fence, we were also fighting deer flies. The fences ran through deep woods. It was a hell of a job. We should have replaced all the fencing right away.” They are still on the farm.
The Stearns History Museum has a collection of barbed wire. Curator of Collections Adam Smith took me to the museum’s big shed in Heritage Park and showed me a large wire donation from Robert “Bob” Diederich. Bob told Steve Penick, head archivist, the collection is from someone Diederich knew who worked for Stearns County. As he traveled the county, he picked up rusting barbed wire from area farm fields and pastures.
The museum also had three strands of wire from Bowlus resident John Maciej and a small strand from Michael Becker, Luxemburg.
As a rural historian, I found I just couldn’t help but photograph the cattle fenced in the pasture near Kraemer Lake and then the barbed-wire wreath I, quite by accident, drove by in Farming Township — and then I just had to write this story.
This column is the opinion of Marilyn Salzl Brinkman. Write to her at Brinkman1943@gmail.com or the St. Cloud Times, P.O. Box 768, St. Cloud, MN 56302.
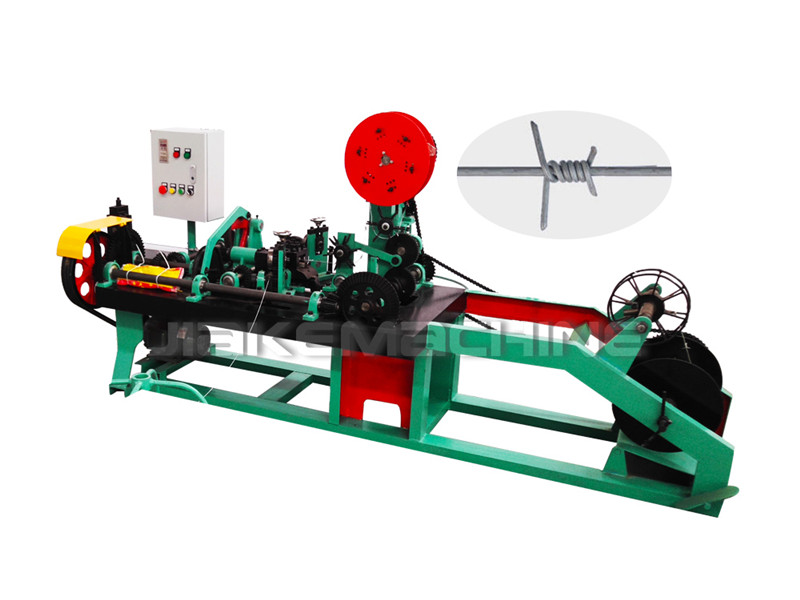
Roll Mesh Welded Machine Early St. Joseph jail used as home, then quilt shed